An international food manufacturer developed a new, vegan food product in its laboratory. It now wanted to industrialize this process and transfer it to mass production. Its priorities were sustainability, energy efficiency, high throughput, and a compact layout. For this reason, the producer did not want to install a standard plant, but a plant optimized for its processes and requirements. It was looking for a development partner who would provide it with the best possible support for the analysis, design, and specification of the new plant.
Thanks to many years of experience in process optimization and in the design, specification, and development of production machinery (including for the food industry) as well as the availability of all the required specialist disciplines, Helbling was able to evaluate different production technologies and organize the necessary function tests (internally and on site with suppliers) within a very short time.
Based on this preliminary work, the food manufacturer is now able to evaluate and optimize the mass production process and can then specify and procure the production plant together with Helbling.
Key Figures
- Mass production with up to 30,000 units per hour
- Guaranteed flexibility for different products and recipes
- Fully automated production for 24/7 operation
- Integration into upstream and downstream production plant
- Hygienic design and customer-specific standards
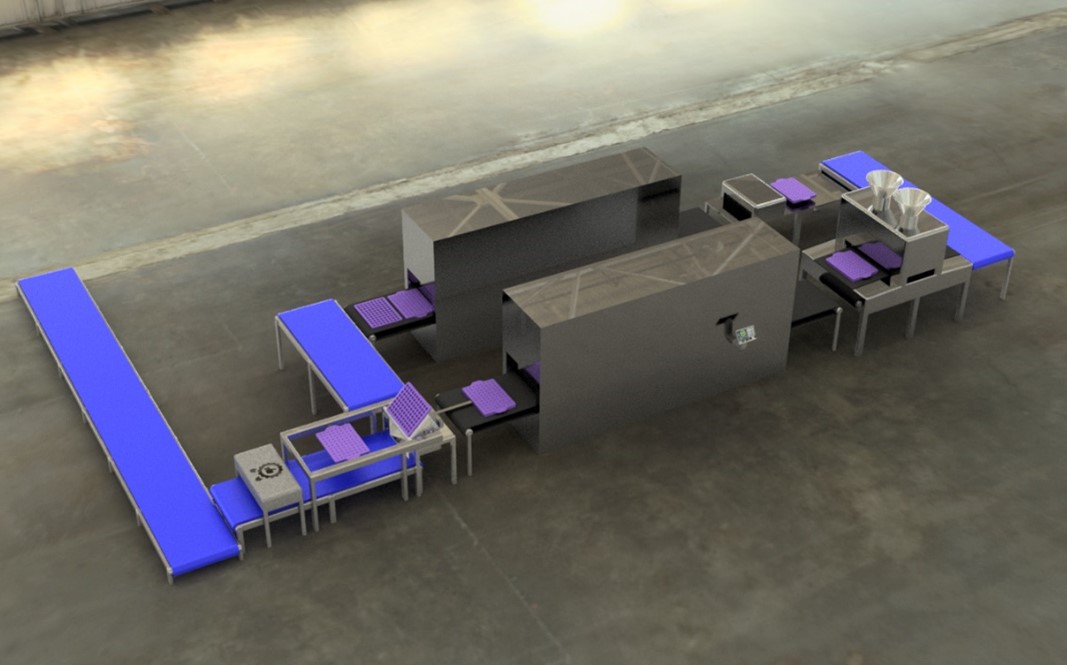
Our Contribution
- Assembly and management of a specialist team
- Analysis of the system and drafting of requirements
- Systematic search for ideas for different production technologies
- Evaluation of possible suppliers/partners for trials and process development
- Carrying out of trials at Helbling
- Organizing and supporting of trials with selected suppliers
- Evaluation of results and prioritization for further development
- Development of scalable concept variants of the production plant including layout, cycle time, and cost considerations
- Drawing up of a comparative analysis with regard to sustainability based on a PCF analysis (Product Carbon Footprint Analysis)
- Creation of a quality assurance, cleaning, and maintenance concept
- Carrying out of a risk assessment for personal safety
- Summarizing of the results and handover of the project to the customer for development of the mass production process for the food product