Industries
Experts in development departments are regularly confronted with questions relating to the manufacturing costs of a product. While it is easy to determine the manufacturing costs of a series product from a company's own product range, it is quite different for the costs of competitor products, purchased components, or alternative concepts. These cost estimates are complex: manufacturing costs of a competitor's product or a calculation from an external supplier cannot be read from an internal system. But what would it mean if this information were available and if it were also possible to optimize these costs? A proven methodology is used in Helbling's day-to-day operations to implement these processes reliably.
Questions about manufacturing costs will inevitably arise during product development and can take up a lot of experts’ time. These usually include the following:
- How close are we to the target price?
- Where are the manufacturing costs of our product in relation to the competition?
- What are the costs of purchased components? Are these possibly overpriced?
- What are the advantages of relocating production?
- What are the effects of quantity scenarios?
Helbling has established a systematic approach to determining and optimizing manufacturing costs. Projects across various industries have already been successfully initiated with this. Some examples are given below as part of the schematic illustrations.
Step 1: Determination of manufacturing costs
The basis here is that the cost drivers of existing products or new products to be developed are identified with the help of a database-driven cost calculation. Helbling uses the DFMA® tool from Boothroyd Dewhurst, among others, for this purpose. Calculations can be carried out based on initial concept sketches, in the form of fully developed 3D CAD data with drawings or as an existing assembly, for example from a competitor. To determine the manufacturing costs, the premises of the calculation, such as production location and quantities, are defined with the customer at the beginning. This information is relevant for selection of production resources and determination of the degree of automation. Estimates can then be made from quantities of one up to millions of units. The tool can be used to determine the manufacturing costs of a component by entering data relevant to the manufacturing costs, such as size, complexity, material, and manufacturing method. In addition to the production of individual parts, assembly and testing steps can also be displayed.
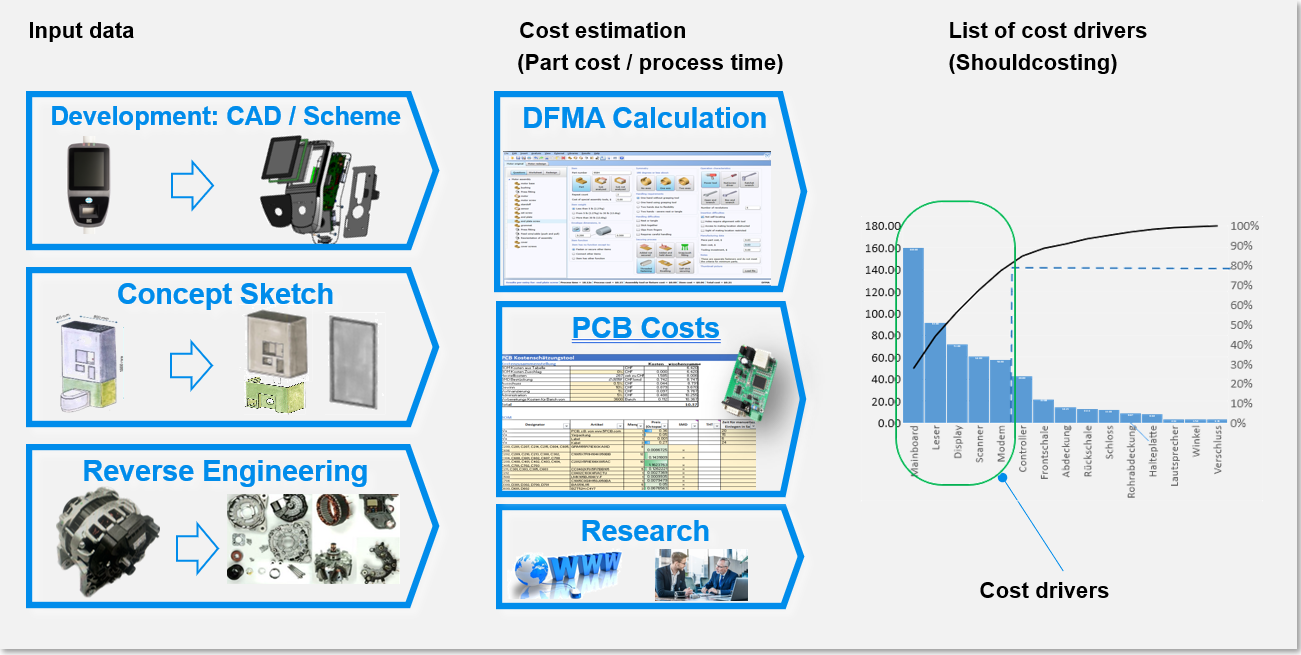
The DFMA® tool from Boothroyd Dewhurst generates both part costs (design for manufacturing) and assembly costs (design for assembly). This allows the total manufacturing costs of a product to be determined. Everyday experience shows that the costs for complex purchased components should also be researched, inquired about, or found out through expert discussions.
As shown graphically in Figure 1, the cost determination can be concluded with an analysis. The determined costs of components, assemblies, and processes can be evaluated according to their relevance. Helbling uses Pareto analysis, which enables cost drivers to read off easily due to graphical representation.
This achieves an essential step: the manufacturing costs of a product are known and can be displayed and analyzed at the levels of components, assemblies, and assembly steps.
Step 2: Optimization of manufacturing costs
The question "What next?" can be discussed and answered individually depending on results and expectations. If cost expectations have been met by now, then the goal has already been reached at this point. If there is a need to optimize or reduce costs, there are various established approaches in everyday R&D. These are shown qualitatively in the following graphic as a function of effort and potential with a further description below.
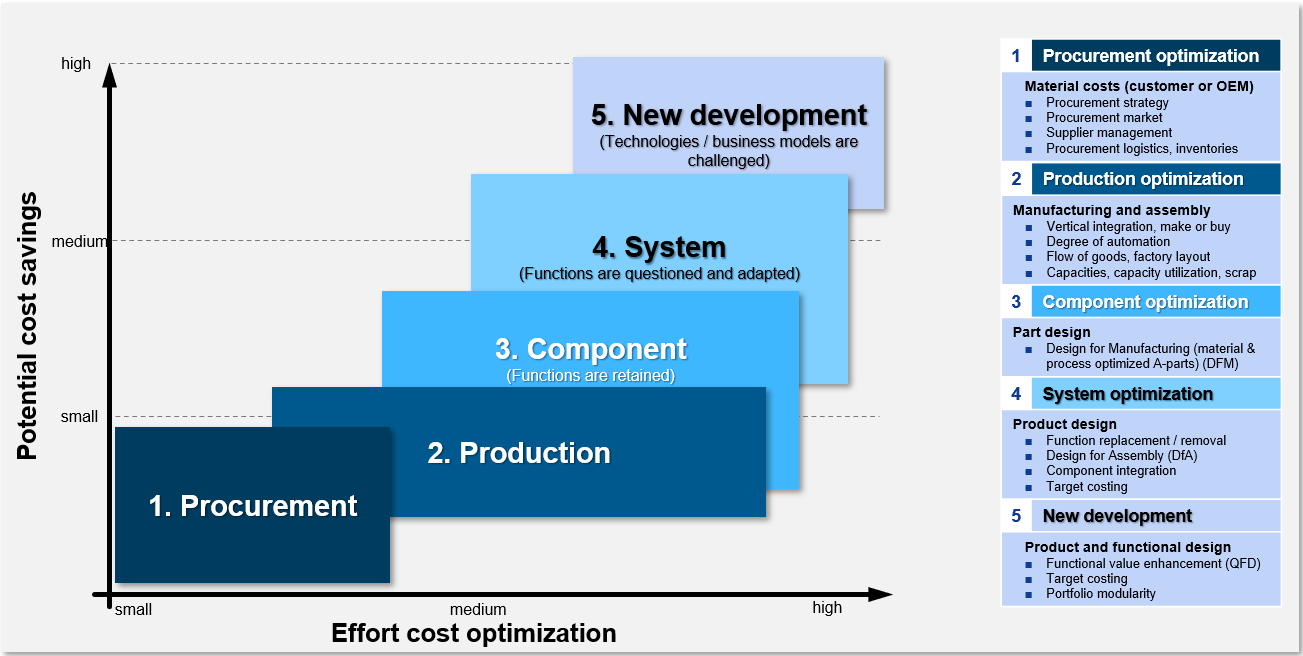
Depending on the challenge, optimization may be required in one or more areas. It is advisable to define ambitious goals so as not to limit the horizon too much from the outset. In abstract terms, the five stages in Figure 2 offer a systematic approach to optimization options. For complex products, different approaches can also be selected in practice for the different assemblies of a product, depending on the desired cost savings target.
Five approaches to cost optimization:
1. Procurement optimization:
Procurement optimization relates purely to the suppliers. The parts and the product remain unchanged. There are various options here:
I. Market analysis: An analysis of the global procurement market makes it possible to identify cheaper and, ideally, higher quality suppliers. Here, the procurement analysis of a component shown in Figure 3 can provide added value by exploiting the different hourly rates of different countries for cost optimization.
II. Negotiation strategies: The manufacturing cost analysis reveals the theoretically possible costs. This knowledge can be strategically decisive for negotiations in order to reach an agreement with suppliers on the best conditions. This makes it much easier to estimate the supplier's room for maneuver.
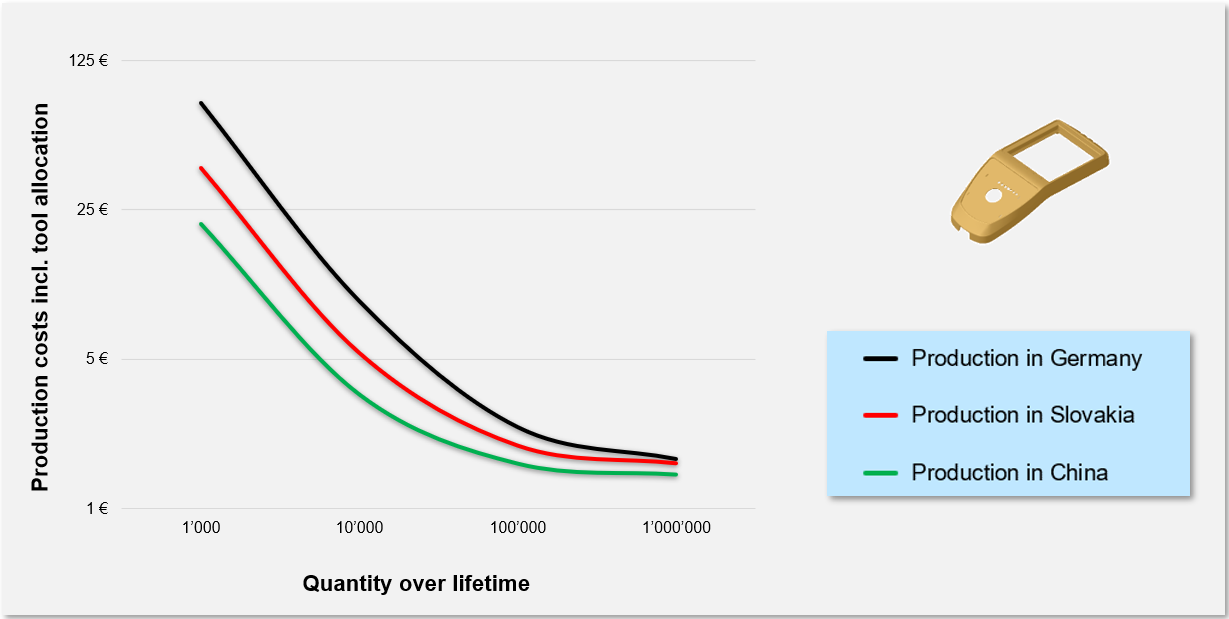
2. Optimization of production:
When optimizing production, assembly and handling steps as well as the technologies used in production are analyzed. The product and parts remain unchanged, but efficiency is increased by minimizing unnecessary steps.
I. Process analysis: The production process is analyzed in detail. Inefficient or superfluous steps can be identified and optimized if necessary.
II. Automation: The potential for automation or an increase in the degree of automation can also be determined with the help of the DFMA® tool. This allows specific savings and investment requirements to be estimated and compared.
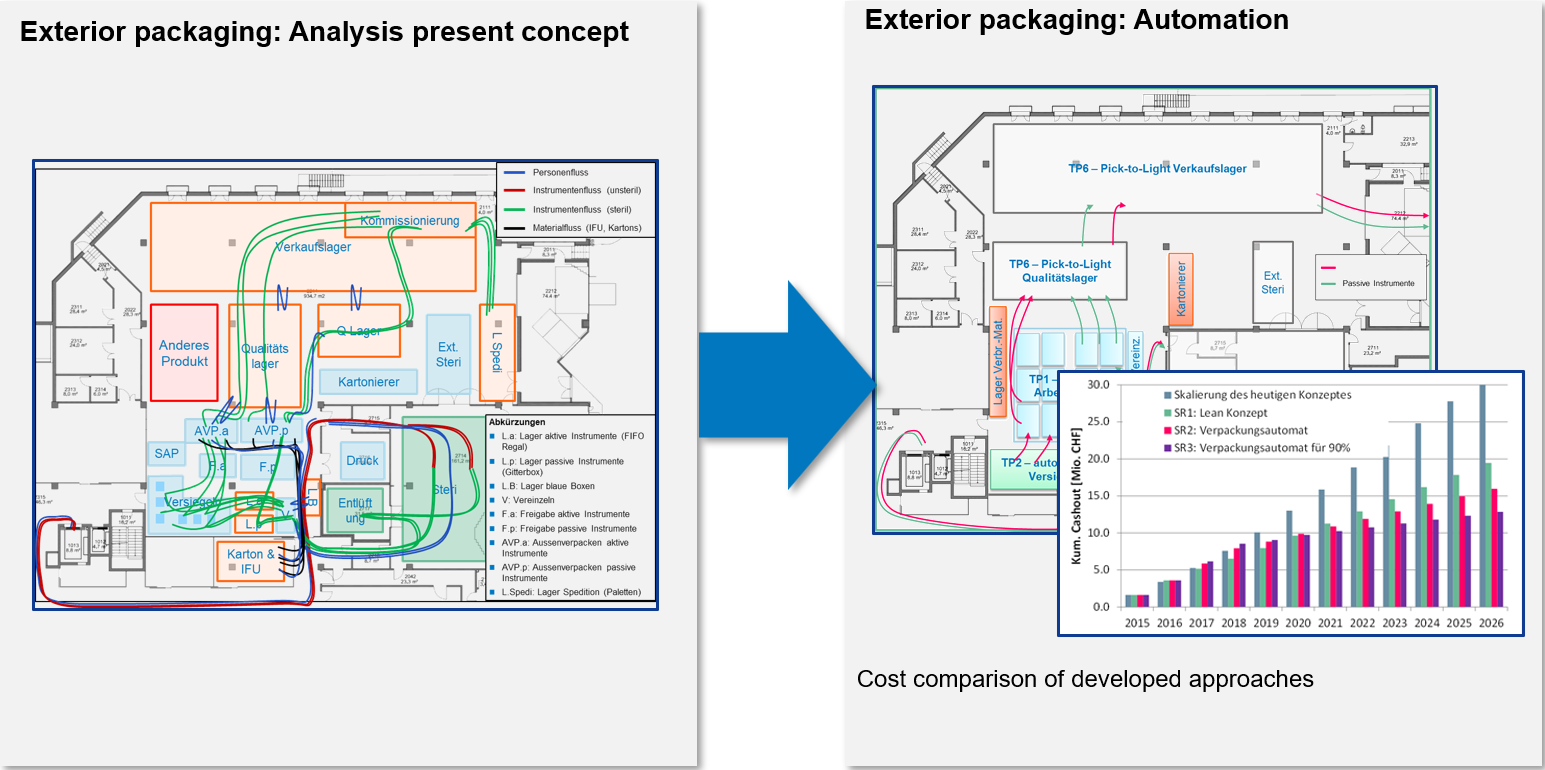
3. Optimization of components:
In this step, individual components are specifically optimized. Depending on the method, it is possible that individual parts can be adapted to achieve lower manufacturing costs.
I. Design review: By analyzing the design, it is possible to identify potential improvements in terms of material consumption, durability, and costs.
II. Material selection: Material costs are a significant factor in manufacturing costs when it comes to larger and heavier components or expensive materials in particular. Cost-effective yet high-quality alternatives must be chosen for optimization.
III. Technology selection: Depending on the number of units required, the manufacturing process can have a major impact on costs. An example of this is shown in Figure 5. The selected component fulfills the same function in each case. The design was adapted for the respective manufacturing process. The calculated costs are plotted based on the quantities for the different manufacturing processes.
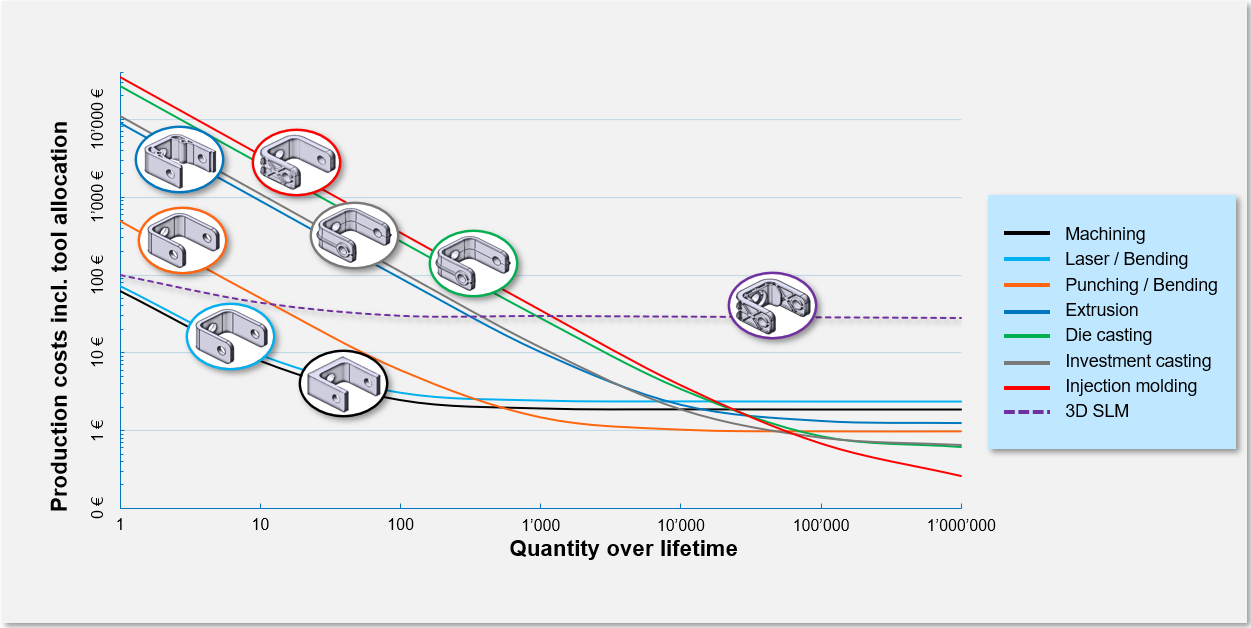
4. System optimization:
In system optimization, complete assemblies are analyzed and optimized if necessary. Ideally, the number of components can be reduced and/or the assembly time improved.
I. Analysis of existing systems: By conducting in-depth analyses of the existing system, experts can identify inefficient processes or obsolete technologies.
II. Component integration: Combining several functions in a single component can reduce the number of components, which in turn can lower material and manufacturing costs. In addition, interfaces are minimized, thus increasing reliability.
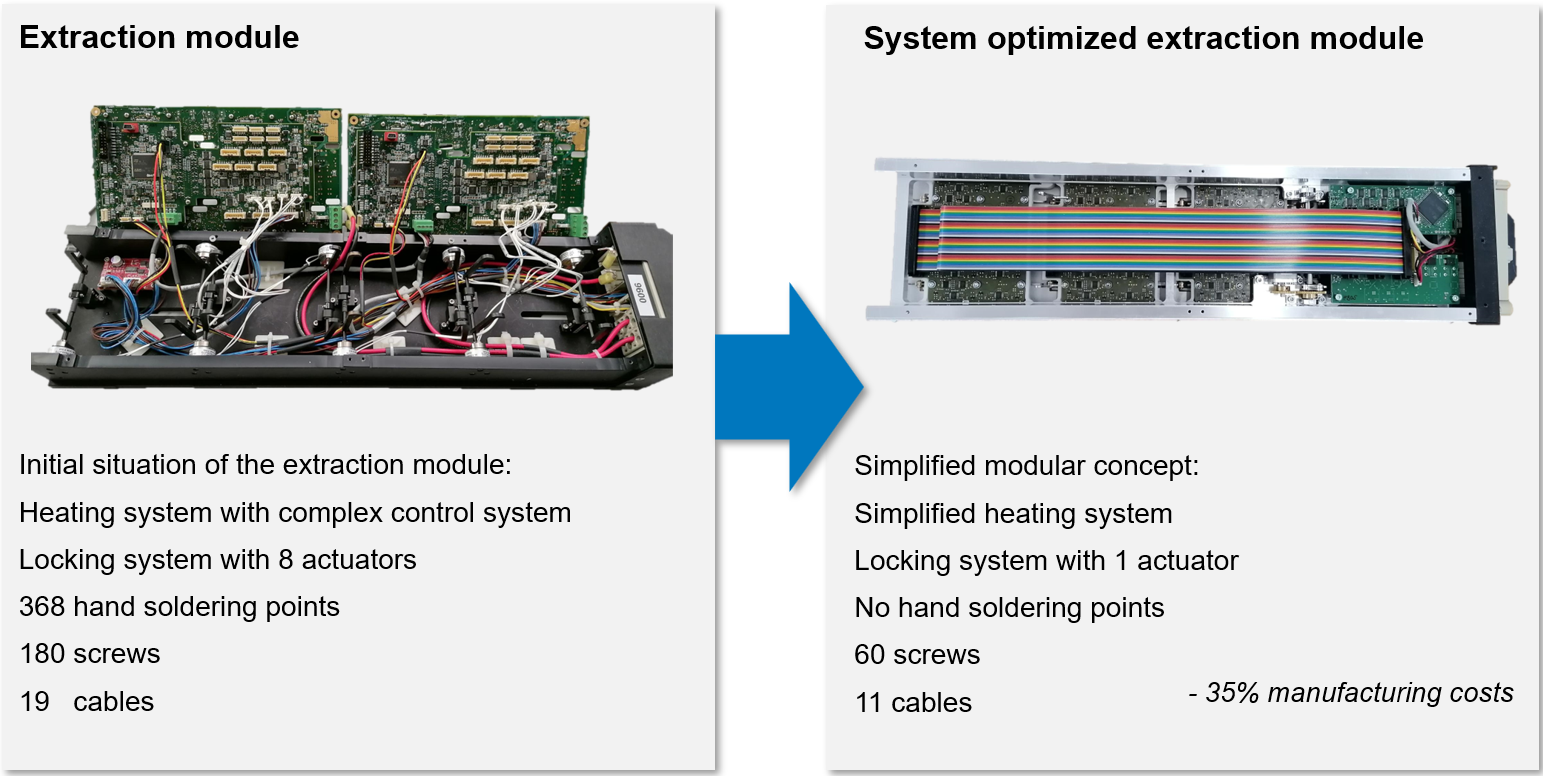
5. New development:
New development of an assembly, a module, or a complete product opens up completely new dimensions in the optimization of manufacturing costs. In the example shown in Figure 7, for example, the costs could be reduced to under a third of the original cost by changing the sensor technology:
I. Implementation of new technologies: System efficiency can be increased by identifying and implementing alternative technologies. However, this involves changing fundamental properties.
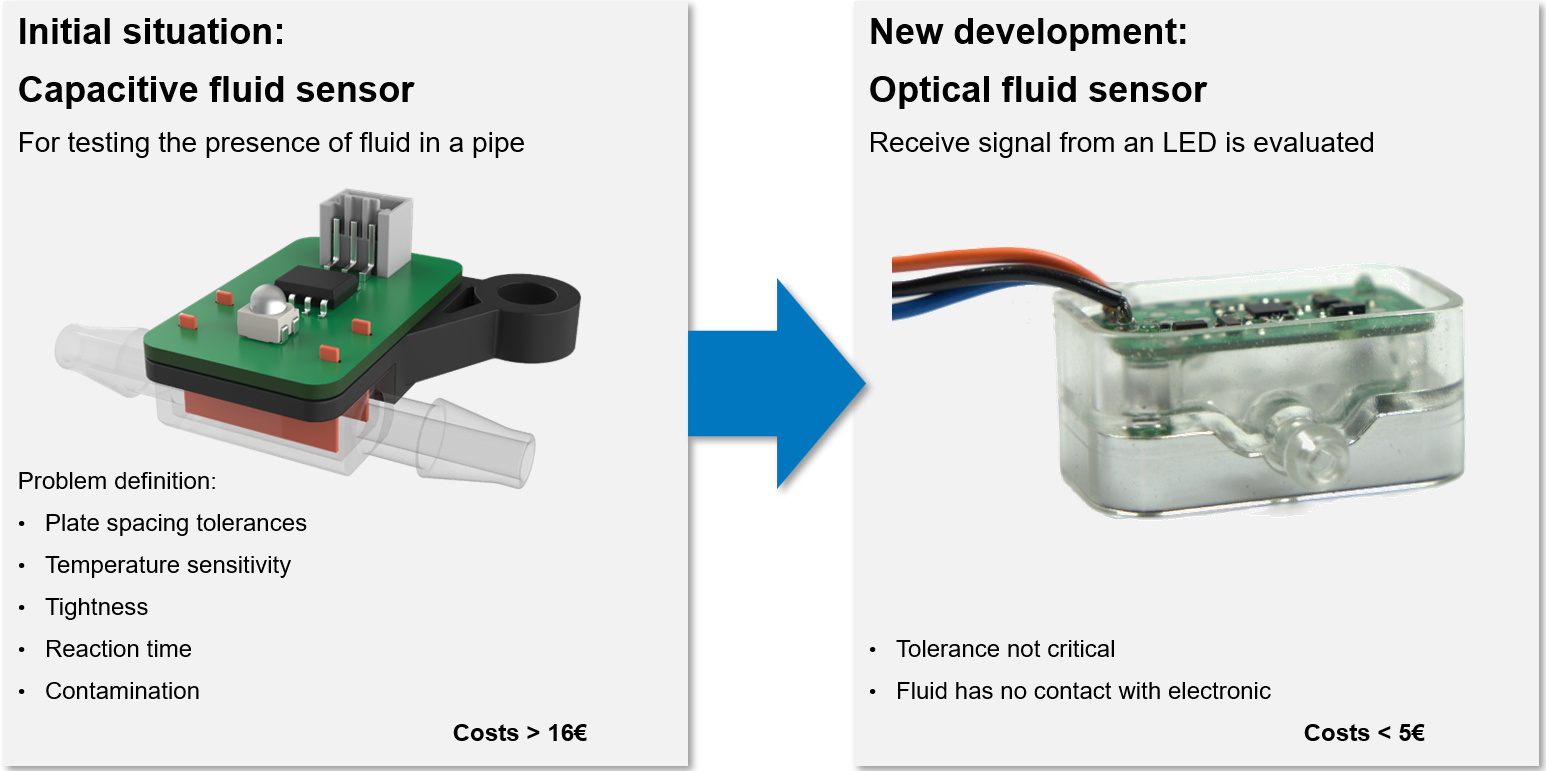
Optimization or reduction of manufacturing costs: The basic process is usually similar: In the first step, the manufacturing costs are determined. Cost drivers can then be determined according to the Pareto principle. There are then various approaches for optimizing or reducing manufacturing costs. It must be decided on a case-by-case basis which approach is the best in practice depending on the task and the acceptable level of effort.
Summary: Cost control is a question of method
Database-driven cost calculation is fundamental when it comes to efficiently getting manufacturing costs under control. In addition, a whole range of options and methods are available for optimizing costs. These can be applied to procurement, production, components, or the system itself. Alternatively, the decision can be made to take a chance on a new development. Helbling has many years of experience in advising and supporting clients in this process.
Authors: Thomas Rümmelin, Johannes Eckstein
Main Image: Helbling